Gas Detection of Tank Farms and Liquefied Gases
RC Systems’ Recommendations:
Pressure Tanks
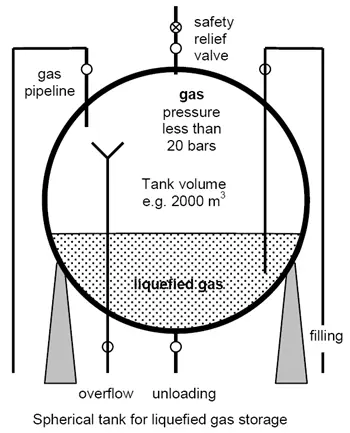
Pressure tanks are equipped with level indicators with alarm trips along with temperature sensors to continuously measure the interior temperature and activate a cooling sprinkler system in case of a temperature alarm.
Safety relief valves control the internal pressure; releasing the gas into the atmosphere or a flare system to be burnt. Either of these processes means costly loss of product along with leading to a potential explosion of toxic gases into the atmosphere leading to a need for toxic and combustible gas detection.
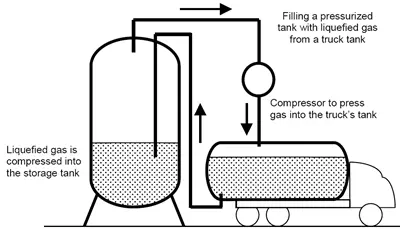
Common Gases in Pressure Tanks
Typical gases stored in pressure tanks are ammonia, amines such as methylamine, dimethylamine, ethylamine, trimethylamine, C3/C4-hydrocarbons such as propane, cyclopropane, propylene, butanes, butylenes, and butadiene, mixtures of propane and butanes called LPG (liquid petrol gas), ethyl chloride, ethylene oxide, chlorine, dimethyl ether, methyl chloride, phosgene, sulfur dioxide, nitrogen dioxide, and vinyl chloride.Cryogenic Tanks
When the liquefied gases have a vapor pressure above 25 bar the containment systems have an increased danger risk. In this case, Cryogenics is the method for obtaining the liquefied gases: Cryogenic means cooling the gas below its boiling point results in liquefaction.Cryogenic tanks require a complex cooling system and are therefore more expensive than pressurized storage tanks. However, cryogenic tanks are also safer since liquefaction occurs at atmospheric pressure. The combination of pressurized and cryogenic containment techniques are quite common.
More and more gas stations and truck stops now have cryogenic LNG storage tanks to support LNG powered vehicles. Gas detection is very important for this application since LNG is odorless and invisible. Odorants the utility providers commonly add to natural gas cannot be added to liquefied methane. Low temperature cryogenic tanks are heavily insulated and much of their volume is insulation only. These tanks contain liquefied gases such as argon (- 186 °C), ethane (- 88 °C), ethylene (- 104 °C), helium (- 268 °C), methane (-161 °C), oxygen (- 183 °C), and nitrogen (- 196°C) at temperatures near their boiling point and atmospheric pressure. Besides oxygen and nitrogen, ethylene is one of the most commonly used products world-wide and many tank farms store ethylene which should be monitored with gas detection.
Atmospheric Tanks
Atmospheric tanks are used for materials which are liquid under normal conditions. Typical atmospheric tanks are used for flammable liquids (e.g. methanol, toluene, xylene), and hydrocarbon mixtures (e.g. gasolines, kerosene) produced in the refineries. Atmospheric tanks normally have wall thicknesses supporting filling pressures only up to .1 bar above atmospheric pressure. Loading and unloading of tanks with a fixed roof cause pressure differentials and require relief valves with breathing to the ambient atmosphere. Atmospheric breathing is through flame arrestors to avoid flash-back into the tank. Vapors may also be fed through flame arrestors to a flare system and sometimes they are re-condensed. Since the vapor pressure of liquids is lower than atmospheric pressure, there is an inert blanket of nitrogen (or other inert gases) added so there is always a small over-pressure against atmosphere preventing air access into the tank. Tanks with roofs floating directly on the liquid surface are also sometimes used.Is the gas detection system needed for bulk storage of toxic and/or flammable substances, liquefied or pressurized? National laws and regulations require high safety standards when the amounts of dangerous goods exceed a given limit. NFPA says: Continuously monitored low temperature sensors or flammable gas detection systems shall sound an alarm at the plant site and at a constantly attended location if the plant site is not attended continuously. Flammable gas detection systems shall activate an audible and a visual alarm at not more than 25 percent of the lower flammable limit of the gas or vapor being monitored. (NFPA 59A, Standard for the Production, Storage, and handling of liquefied Natural Gas(LNG), Chapter 12.4.2 Gas Detection)
Tank farms require gas detection primarily for explosion protection and early leak detection. Explosion protection means tripping alarms at concentrations of 20% to 40% LEL and promptly activating countermeasures at the site (informing operators, technicians and fire brigade) and/or switching countermeasures (closing solenoid valves, activating cooling showers, water sprayers). Tank loading and unloading might be accompanied by large leaks when connecting the appropriate pipes to tank trucks. Early leak detection is accomplished by detecting and alarming at lower concentrations (e.g. 10 % LEL). Even with temperature and pressure gauge sensors, small leaks (hairline cracks) are difficult to detect without gas detection. However, over long periods these small leaks mean costly loss of product and may even become a large leak with hazardous consequences. Tank farms must have a safety distance between the tanks in case of a fire, the probability of affecting adjacent tanks is minimized. Some applications even strip out the cooling water to monitor for dissolved flammable, e.g. ethylene.
Gas Detection of Tank Farms and Liquefied Gases (PDF version)
Wired Gas Detection System |
||
Gases | Detectors | Controller |
ammonia, amines, sulfur dioxide, chlorine | SenSmart 5100/6100 EC | ViewSmart 400 (Up to 4 points) ViewSmart 1600 (Up to 16 Points) ViewSmart 6400 (Up to 64 Points) |
Flammable Gases | SenSmart 5300/6300 IR | |
Fence monitoring to avoid flammable gases leak and drift into safe areas | Quasar 900 Open Path | |
Wireless Gas Detection System | ||
Gases | Detectors | Controller |
ammonia, amines, sulfur dioxide, chlorine | SenSmart 7100 EC | WNR WaveNet Receiver |
Flammable Gases | SenSmart 7400 IR | (Up to 32 Points) |